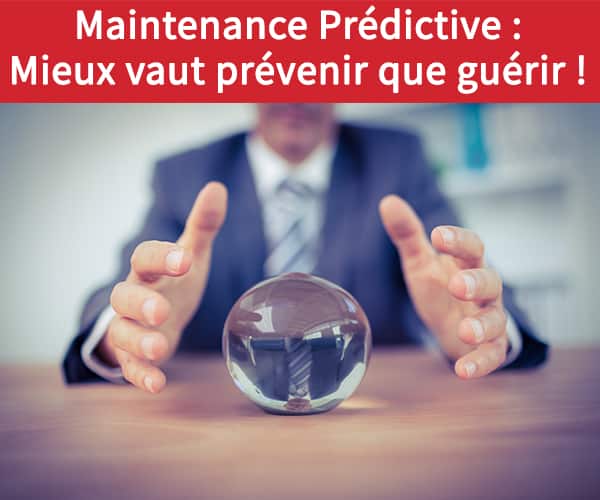
- Analytics
- IoT
- Maintenance
Maintenance Prédictive : Mieux vaut prévenir que guérir !
« Mieux vaut prévenir que guérir ! » Cette maxime vaut également pour les activités de maintenance. À l’heure du Big Data, de l’industrie 4.0 et de l’internet des objets, de nouvelles technologies permettent de faire évoluer les stratégies de maintenance du curatif vers le prédictif. Une étude menée par l’institut de recherche Aberdeen Group, en juin 2017, montre que 37% des entreprises de service envisagent d’inclure des outils d’analyse prédictive dans leurs activités de maintenance. Dans cet article, nous allons vous présenter en quoi consiste la maintenance prédictive et quels sont les bénéfices que vous pouvez en retirer pour votre entreprise.
Maintenance curative, préventive ou prédictive ?
Commençons par quelques définitions. La maintenance curative (ou également appelée maintenance corrective) consiste à intervenir pour réparer un équipement ou une machine, une fois qu’une panne s’est produite. La maintenance curative ne permet pas de prévoir ou d’anticiper une panne. Elle n’intervient qu’après coup. La maintenance préventive est une approche différente. Ici, il s’agit de prévoir des actions régulières sur un équipement ou une machine afin d’assurer son entretien dans la durée. La maintenance préventive consiste donc à intervenir pour anticiper une panne possible en se basant essentiellement sur l’estimation du cycle de vie d’un équipement. Le problème est souvent le timing : on décèle une usure ou un défaut, la machine peut continuer à fonctionner encore un certain temps, mais à titre de précaution, on procède tout de même au remplacement de la pièce. De fait, la maintenance préventive entraîne souvent une dépense qui aurait pu être évitée ou tout au moins reportée. La maintenance prédictive est, selon la définition donnée par l’encyclopédie Wikipédia, « une maintenance conditionnelle basée sur le franchissement d’un seuil prédéfini qui permet de donner l’état de dégradation du bien avant sa détérioration complète ». Fondée sur l’analyse de données collectées grâce à des capteurs intelligents positionnés sur l’équipement, elle permet de pousser à bout la logique du « juste à temps » et ainsi d’optimiser l’usage d’une machine avant de procéder à sa réparation ou à son remplacement, juste avant qu’une panne ne se produise. La maintenance prédictive permet de prévoir les incidents techniques plutôt que de les subir. Grâce à cette stratégie, il est ainsi possible de programmer à l’avance des interventions et ainsi d’éviter une immobilisation imprévue d’un équipement ou d’une machine. Elle pousse donc les choses un cran plus loin que la maintenance préventive.
Comment faire de la maintenance prédictive ?
Pour mettre en place une stratégie de maintenance prédictive, il faut d’abord installer des capteurs sur les équipements concernés. Ces capteurs vont permettre de collecter en continu des données sur l’état de fonctionnement des machines. Ces données vont ensuite être analysées et modélisées par des programmes informatiques (des algorithmes). Ces derniers vont ainsi, en fonction de paramètres spécifiques, établir quels sont les comportements normaux attendus de la part des équipements, ainsi que des seuils d’alerte permettant d’avertir sur une panne imminente.
Des capteurs intelligents
Il existe tout un ensemble de capteurs industriels divers et variés. Les équipements et machines modernes en sont de plus en plus équipés. On recense ainsi des capteurs pour :
- La détection de défauts par ultrasons
- L’analyse thermographique par infrarouge
- L’analyse vibratoire
- L’analyse des fluides
- L’analyse des huiles
- L’analyse spectrale
Intelligence Artificielle et prédictions
Ensuite, pour mener à bien votre projet de maintenance prédictive, il vous faut déployer les outils analytiques qui vont vous permettre de découvrir ce qui se cache dans les données relevées par les capteurs. On entre ici dans le domaine de l’Intelligence Artificielle. Les algorithmes vont traquer et analyser les données caractéristiques d’une panne. À partir de là, ils vont modéliser des combinaisons de données similaires, des schémas de panne, et fixer des seuils d’alerte en conséquence. Dès qu’une de ces combinaisons réapparaîtra, le système considèrera qu’une panne va avoir lieu de manière imminente. À l’aide d’un logiciel de gestion de répartition, tel que Praxedo, connecté à ces outils de supervision, l’entreprise peut ainsi automatiser la prise de décision sur les opérations de maintenance.
Intégration des systèmes d’information
Notez que l’intégration des différents systèmes d’information concernés est importante pour la réussite d’un programme de maintenance prédictive. Il faut « désiloter » les données de maintenance et les centraliser afin de faciliter leur exploitation par les outils analytiques. Ce type de démarche est aujourd’hui facilité par le développement de la technologie de l’hébergement en nuage. D’ailleurs, l’étude d’Aberdeen Group mentionnée en introduction indique que les entreprises utilisant des technologies d’analyse prédictive pour leur maintenance sont 33% plus performantes dans la création d’une vision unifiée de leurs données issues de l’ensemble de leurs systèmes d’information.
Coûts et bénéfices de la maintenance prédictive
Mettre en place une stratégie de maintenance prédictive permet de réaliser des économies significatives par rapport à la maintenance curative ou préventive, car les tâches ne sont réalisées qu’au moment approprié. La maintenance prédictive permet aux services de maintenance d’anticiper le moment précis où la panne va avoir lieu et ainsi de ne lancer une intervention qu’en cas de nécessité avérée. Elle permet ainsi de trouver le juste équilibre pour intervenir : ni trop tôt, pour réduire les coûts, ni trop tard, pour éviter une panne.
Des investissements de départ nécessaires…
En premier lieu, déployer un programme de maintenance prédictive peut représenter un coût significatif pour votre entreprise. Il va falloir vous doter des capteurs de données nécessaires pour assurer la surveillance continue de vos équipements et machines et acquérir ou développer les outils analytiques dédiés à l’exploitation de ces données. En outre, il faut également prendre en compte le coût de formation de votre service de maintenance pour lui permettre de maîtriser ces nouveaux outils d’analyse de données. Ensuite, il faut prévoir le temps nécessaire pour développer et déployer le programme dans votre entreprise.
… Pour des bénéfices opérationnels importants
Mais en contrepartie, les bénéfices sont énormes, notamment sur le long terme :
- Une diminution drastique des pannes et donc des temps d’immobilisation des équipements ;
- Une meilleure surveillance des équipements permettant d’anticiper des incidents mineurs pouvant entraîner des problèmes plus importants ;
- Une utilisation optimale des équipements (jusqu’au moment précis où la panne va se produire) et un allongement de leur durée de vie ;
- Une amélioration de la fiabilité des équipements et donc une optimisation de la production ;
- Une meilleure planification des interventions, et donc une meilleure préparation des équipes de maintenance ;
- Une meilleure gestion des stocks de pièces de rechange ;
- Une réduction des frais de maintenance et des coûts liés à l’arrêt des machines.
A titre d’exemple, le cabinet de conseil Roland Berger a produit, en 2014, une étude indiquant que les entreprises du secteur de l’énergie ayant mis en place des programmes de maintenance prédictive ont ainsi réussi à éliminer pas moins de 75% des pannes sur leurs équipements. Cela illustre parfaitement et concrètement les avantages à mettre en place de tels programmes, notamment dans le secteur industriel où les interruptions de production liées à la maintenance peuvent très vite coûter très cher aux entreprises. Alors, quand est-ce que vous passez au prédictif ?
Nos articles similaires
-
- Gestion de répartition
- Maintenance
- automatisation
- eaux usees
Automatisation du traitement des eaux usées : conseils clés pour gagner en efficacité
26 mai 2022 -
- Gestion de répartition
- Maintenance
- Technicien
Equipements médicaux, passez à la maintenance préventive !
29 septembre 2021