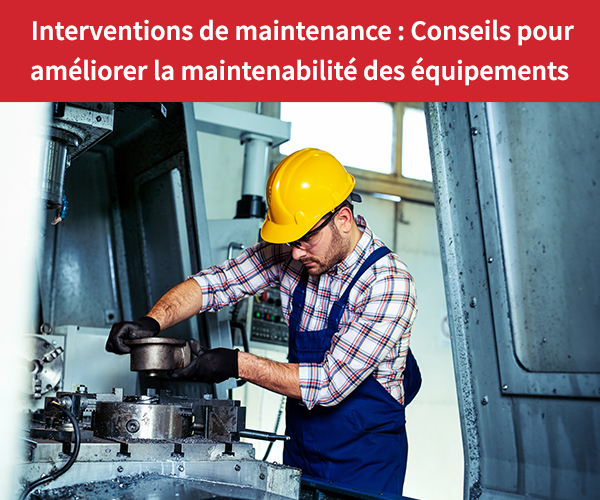
- Gestion de répartition
- Maintenance
- Optimisation
- Productivité
Comment optimiser la maintenabilité de vos équipements
La maintenabilité ou « maintenance by design » consiste à prendre en compte dès la conception d’un équipement les impératifs des équipes de techniciens de maintenance afin de faciliter leur mission. Une optimisation du design permet une diminution des temps et des coûts d’intervention.
Le service de maintenance a généralement pour fâcheuse habitude d’être mis dans la boucle en bout de chaîne. Une fois que le produit a été conçu et distribué, les équipes de maintenance sont formés pour assurer son entretien sans que leur avis ne leur ait été demandé préalablement.
Les concepteurs de bureaux d’études prétendent souvent, à tort, connaître les contraintes et les impératifs des exploitants et des agents de maintenance et négligent de recueillir leur feedback.
Le concept de maintenabilité vise à inverser l’ordre des choses. Dès la phase conception, les équipes de maintenance donnent leurs avis sur la pertinence des choix arrêtés. Peut-on, par exemple, accéder facilement à ce sous-système, le démonter et le remonter ?
Par définition, la maintenabilité est la capacité d’un équipement à être dépanné, dans un temps donné, à moindre coût et selon des conditions spécifiées. Il doit aussi retrouver sa fiabilité initiale.
Annulée cet été, la norme Afnor X 60-500 évoquait, elle, “l’aptitude d’une entité à être maintenue ou rétablie, sur un intervalle de temps donné, dans un état dans lequel elle peut accomplir une fonction requise, lorsque la maintenance est accomplie dans des conditions données, avec des procédures et des moyens prescrits.”
Concilier expérience utilisateur et expérience mainteneur
A côté du principe de maintenabilité, on parle aussi de “maintenance by design”, comme il existe la “privacy by design” dans le cadre du règlement européen sur la protection des données personnelles (RGPD) ou la “security by design” pour la prise en compte des vulnérabilités d’un système en moment de sa conception.
Le design d’un produit doit prendre en compte l’expérience utilisateur (UX) en proposant une interface ergonomique, c’est-à-dire fluide et intuitive. A côté de cette expérience utilisateur, on pourrait évoquer l’expérience du mainteneur, les deux étant liés.
A une époque où la notion d’obsolescence programmée est remise en cause au profit des principes plus vertueux de développement durable, tout ce qui peut être fait pour allonger la durée de vie d’un équipement contribue à l’expérience utilisateur.
Un enjeu économique
L’enjeu est aussi économique. Toute optimisation de la maintenance entraînant une diminution des temps et des coûts d’intervention est bonne à prendre. Ce qui est particulièrement vrai dans l’industrie où l’arrêt d’une ligne de production entraîne pour l’exploitant une perte de temps, une perte de chiffre d’affaires et une perte de crédibilité auprès des clients.
Dans le domaine aéronautique, la maintenance représente son plus gros poste de dépense après le kérosène. Selon une étude menée de l’IATA (International Air Transport Association), le coût moyen de la maintenance pour une compagnie aérienne est estimé à environ 1 070 dollars par heure de vol.
Du choix des composants à la documentation technique
Le chantier de la maintenabilité démarre par le choix des composants qui doivent être robustes, fiables, durables. D’autres éléments sont pris en compte comme l’accessibilité des organes d’usure, la standardisation et la disponibilité des pièces détachées. La recherche de maintenabilité peut aussi conduire à introduire la notion de fonctionnement en mode dégradé.
La partie documentation – plans techniques, manuel de procédures… – est également essentielle. Idéalement, elle doit être rédigée au moment de la conception de l’équipement quand l’équipe projet est totalement mobilisée. Au risque, sinon, de voir sa rédaction bâclée quand elle s’effectue en fin de course.
De même, afin d’éviter toute déperdition d’information, il s’agira de formaliser les opérations de maintenance préventive dans des cahiers d’entretien. A quelle fréquence ces actions devront être effectuées ? Par qui et selon quel mode opératoire ?
La réalité virtuelle au service de la maintenance by design
La simulation numérique est une autre piste prometteuse pour faciliter la maintenance by design, notamment avec l’apport des technologies de réalité virtuelle et de réalité augmentée. Plongé dans un univers immersif, un expert de la maintenance va pouvoir tourner autour du prototype, reproduit à l’échelle 1, apprécier ses dimensions réelles, bien mieux que devant un écran même si celui affiche une image 3D.
Une fois le produit commercialisé, ces nouvelles technologies immersives participent à la formation des techniciens de la maintenance, un autre facteur-clé de la maintenabilité. Coiffés d’un casque de réalité virtuelle, ils pourront répéter à l’envi les gestes à accomplir sans craindre une mauvaise manipulation. Dans “la vraie vie”, ils seront ainsi totalement opérationnels dès leur première intervention.
La réalité virtuelle présente aussi l’avantage de simuler des événements exceptionnels – incendie, coupure d’électricité… – ou des conditions météorologiques particulières – de nuit, sous une averse, une tempête neige, dans le brouillard. Des cas de figure auxquels aucun manuel technique ou formateur ne pourra préparer.
L’internet des objets pour le feedback utilisateur
L’internet des objets joue également un rôle clé dans la maintenabilité. En plaçant des capteurs sur son équipement, un fabricant sait précisément et rapidement comment ses clients l’utilisent sans attendre les réclamations ou les retours.
Cette boucle de rétroaction (feedback) lui permet de préparer ses équipes de maintenance aux pannes prévisibles mais aussi d’apporter les évolutions nécessaires dans la prochaine version de sa machine.
FMDS, MTTR, MTBF… Les indicateurs de suivi
Il faut non seulement mettre en place les conditions d’une meilleure maintenabilité mais aussi mesurer derrière les progrès accomplis. Une analyse dite de Fiabilité Maintenabilité. Disponibilité Sécurité (FMDS) repose sur quelques indicateurs clés, parmi lesquels on trouve le temps moyen jusqu’à la réparation (MTTR, Mean Time To Repair) ou le temps moyen entre deux défaillances (MTBF, Mean Time Between Failure).
Les notions de fiabilité, de maintenabilité, de disponibilité et de sécurité sont interdépendantes. En voulant améliorer la maintenabilité d’un équipement, un constructeur peut nuire à sa fiabilité ou le rendre moins sécure.
Un fabricant peut, par exemple, faire le choix d’une conception modulaire afin de faciliter la maintenance – les différents composants se remplacent aisément -, au risque de fragiliser l’ensemble ainsi constitué.
En analysant le coût total de possession (Total cost of ownership, TCO), qui couvre tout le cycle de vie d’un équipement, il conviendra d’arbitrer et de trouver le meilleur compromis possible entre fiabilité et maintenabilité.
Nos articles similaires
-
- Big Data
- Gestion de répartition
- Gestion de répartition
Gestion de répartition et analyse prédictive
13 novembre 2018 -
- Maintenance
- Technicien
- Application mobile
- Gestion de répartition
Comment veiller à la sécurité des techniciens de maintenance
25 novembre 2020 -
- Intelligence artificielle
- Maintenance
- IoT
- Gestion de répartition
Quelles formes de maintenance dans l’usine du futur?
19 février 2019